Construction Material Procurement
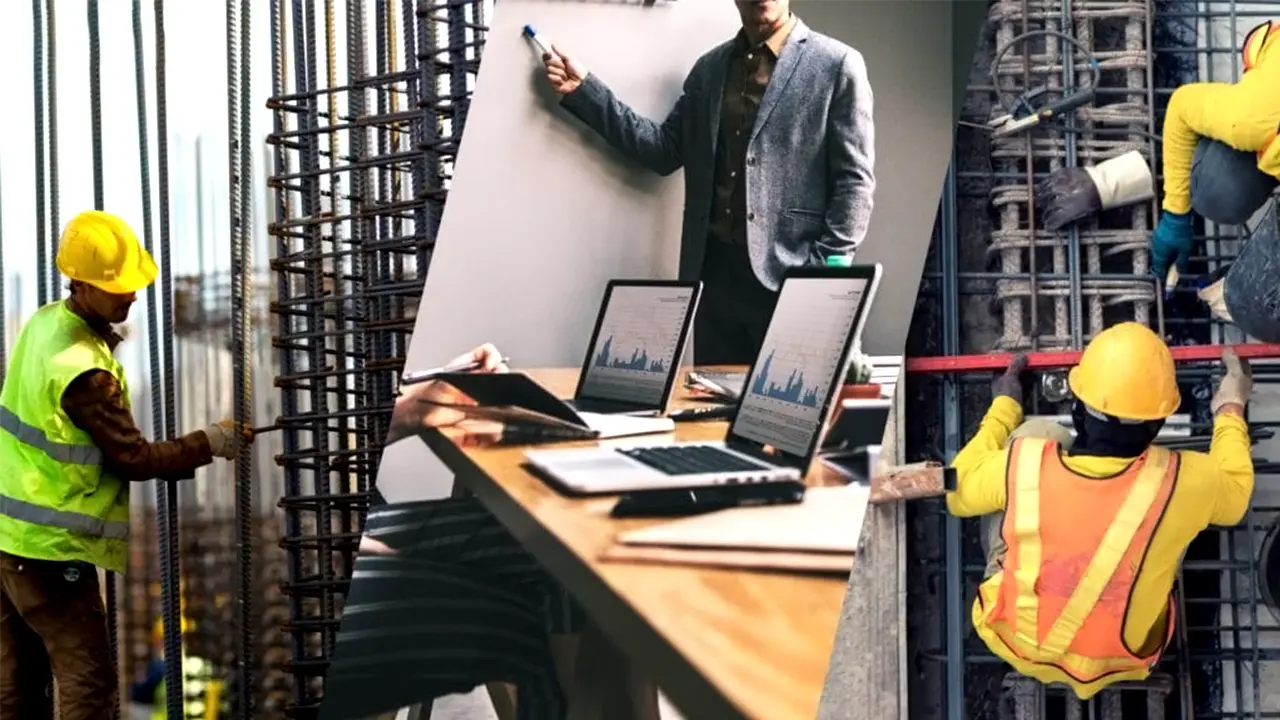
5 Golden Strategies to Improve Construction Material Procurement and Reduce Costs
In construction projects (residential, commercial, industrial), material procurement is a critical factor determining a project’s success. This process, which involves multiple stakeholders, includes selecting materials, placing orders, invoicing, making payments, and delivering items to the site. The main goal of contractors in material procurement is to acquire the best quality materials at the right quantity, time, and cost. Amid ongoing supply chain challenges, this process has become even more crucial.
Challenges and Additional Costs in Material Procurement
Despite being aware of these issues, many contractors lack a precise process or management system for material procurement. This can lead to unnecessary and avoidable expenses, such as:
- Paying premium prices for materials.
- Over-ordering materials.
- Prolonged delivery times.
- Failing to monitor material price fluctuations.
Below, we outline key aspects of the procurement process and strategies to improve it, saving both time and money in construction projects.
1. Incorporate Procurement in the Design Stage
Building strong working relationships with suppliers is an essential requirement for any contractor, regardless of industry segment. Trust, fairness, mutual benefits, and honesty are foundational elements for selecting reliable suppliers during the design phase of a project. However, how can you track a supplier’s performance across various projects?
Using the right tools to document suppliers’ histories, pricing, and reliability is essential. Additionally, based on project specifics, adjusting material specifications can mitigate risks with less reliable suppliers, ultimately reducing costs.
2. Look Beyond Purchase Price
Successful material procurement isn’t just about securing the lowest price. It involves sourcing the correct materials at the best overall value from reliable suppliers. This requires a focus on total cost, not just unit cost.
Total cost includes:
- Reliability of the supplier.
- Availability of materials.
- Transportation and logistics expenses.
- Storage costs.
- Disposal costs, if applicable.
Shifting focus from the lowest price to overall value is a worthwhile strategy that ensures long-term cost savings.
3. Establish Early Agreements with Suppliers
Small and medium-sized contractors relying on day-to-day ordering processes may miss opportunities for better material rates. At the project’s outset, negotiating fixed rates based on required volumes can result in substantial savings.
Agreed rates don’t necessarily mean all materials are delivered at once; instead, they ensure predictable costs over time. Regular monitoring of incoming and outgoing invoices ensures that agreed rates are applied throughout the project.
4. Plan for Effective Procurement Staffing
Many current procurement methods are outdated, relying on emails, text messages, and spreadsheets for tracking. Procurement managers often need to visit sites to verify material deliveries. Depending on the contractor’s size, some companies hire dedicated staff for this role, while others distribute responsibilities among team members.
A proper organizational structure must be established at the company level and adhered to for every project. For example:
- Volume Discounts: Negotiate project-specific material discounts.
- Order Approvals: Management should approve all orders.
- Multiple Quotes: Require three supplier quotes for purchases over $1,000.
Strategic planning and adopting value-based approaches empower procurement teams to unlock potential savings on every project.
5. Choose the Right Technology
Contractors can no longer afford to maintain traditional methods when the construction industry is rapidly adopting purpose-built technology.
The right technology can:
- Connect field teams, office staff, and suppliers.
- Digitize procurement workflows.
- Replace manual activities.
- Enable real-time tracking and management of orders and costs.
Digital procurement platforms like Procore, Buildertrend, or similar tools streamline the ordering, pricing, and tracking of materials. They require minimal training and no extensive IT resources, making them accessible and efficient.
Conclusion
Smart strategies in construction material procurement can lead to significant cost and time savings. These strategies include leveraging new technologies, creating organized team structures, and focusing on total costs rather than just purchase prices. By implementing these approaches, contractors can optimize their procurement processes, minimize risks, and ensure the success of their construction projects.